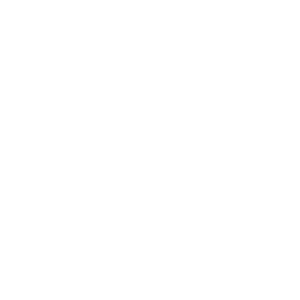
Resources
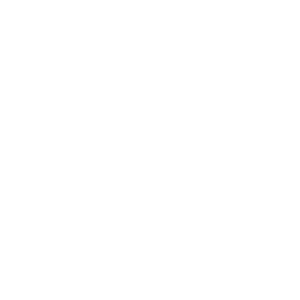
Common Questions Asked of the Pumper SSTS Professional
The answer to this question depends directly on how the household uses the system. Variables such as how many people reside in the home, garbage disposal use, age of the system, how much entertaining is done, etc. affect the time period in which solid waste accumulates in the septic tank. On the average, the septic tank should be cleaned out every two to three years. The Pumper should be able to give you a recommendation once she/he has cleaned the tank. If you have a garbage disposal the septic tank should be cleaned annually.
The cleaning must be done through the maintenance opening (typically a 28-inch in diameter concrete manhole-type cover). Cleaning through this opening allows the Pumper to move the pumping hose over the entire bottom of the tank, removing all the solid waste accumulation. The Pumper can also inspect the inside of the tank for any cracks or infiltration problems as well as checking to be sure that the baffles are in place.
The location of the maintenance hole cover will vary by tank manufacturer. However, the cover typically will be located either in the center of the tank or there will be a cover at each end of the tank. Your Installer may have a location map or your local unit of government may have a location map, often called an as-built.
As wastewater is discharged from the house, the tank will fill back up in a short period of time and then begin to trickle-flow into the next tank or to the treatment area, depending on what type of system you have. The rate at which the tank fills up of course depends on the gallons per day that are discharged to the tank. When onsite sewage systems are sized one of the factors that is included in the calculation is projected gallons per day of water used. The standard applied is 150 gallons per day per bedroom, or 75 gallons per day per person. This daily use takes into consideration water use for entertaining, food preparation, personal hygiene, laundry, dishwashing, etc.
The alarm on your lift station is not a signal to have your septic tanks cleaned although many people seem to think this is the purpose of the alarm. The alarm is alerting you that the lift station pump is not pumping effluent up to the treatment area. A float switch that has failed and is not turning the pump on, a pump that has failed, or no electrical power to the lift station may cause this. If your circuit breaker is in the on position and the pump does not work, your Pumper can repair the problem or direct you to another SSTS professional who offers this service. Minimize your water use until the repair can be made.
Common Questions Asked of the Designer I and Designer II SSTS Professional
The site evaluation will determine the proper location for the new onsite sewage treatment system based on soils, the depth to saturated soil or bedrock, and the natural land slope of the site. The other factors included in the evaluation are the number of bedrooms for the home and the number of water using devices in the home. The documentation you receive will include copies of the soil borings, perc test results, and a sketch illustrating the design.
Before you buy a lot, know exactly where the lot lines are located. Then determine the most desirable location for your home and the best place for the sewage treatment system. Remember that steep slopes, ponds, and marshy areas will construction and drainage problems. Soil borings will be needed at the proposed sites for the house and the treatment area. Be particularly concerned about evidence of a high seasonal water table in the soil. A percolation test does not give you the information necessary to determine the water table. The percolation test only has the ability to tell how well the soil will accept water. At some times, the water table can be observed in the boring holes. Other times, the only evidence of high seasonal water table may be mottled soil that is colored several shades of red and gray. A licensed Designer is your best resource for determining if the lot can support a sewage treatment system as well as a secondary site for future use. Before finalizing any purchase contract, contact the local zoning office to see whether you can get a building permit, including a permit to install an onsite sewage treatment system.
The SSTS industry continues to embrace new technology to improve treatment and provide cost efficiencies. One of the most current areas of interest is pre-treatment. Pre-treatment technologies provide treatment of the wastewater before it is discharged into the soil treatment area (trenches, mound, at-grade), minimizing the work of the treatment area, and possibly extending the life of the system. Some types of pre-treatment include aerobic tanks, peat filters, sand filters, and constructed wetlands. The Designer is an excellent resource for finding out more about the possibilities of new technology applications for your onsite sewage treatment system.
Onsite sewage treatment systems provide adequate treatment of wastewater when they are sited, designed, installed, and maintained properly. One of the most important elements of the site evaluation and installation is maintaining adequate vertical separation between the soil treatment area and the water table. The current requirement in Minnesota is for a three-foot vertical separation. This factor will determine if your treatment area can be installed in the ground, at existing grade, or if the treatment area will need to be a mound to create the vertical separation from the bottom of the rock bed to the water table or mottled soils.
Common Questions Asked of the Installer SSTS Professional
The time it takes to install the system depends on the complexity of the system, but typically the installation will take from one to three days. When an old system is being replaced with a new system, the house occupants do not need to move out of the house. There may a be brief period of time that the Installer will ask you to keep from discharging any waste water from the house while the new line is being hooked up from the house to the new tank.
Like any product we buy, longevity greatly depends on use and maintenance. However, a system that has been properly designed and installed, used in the manner for which was designed, and properly maintained, can be expected to provide service from twenty to twenty-five years, on average. Some parts of the system such as alarms, switches, pumps, and filters will most likely have to be replaced over the lifetime of the system. Each onsite sewage treatment system is designed specifically for an individual site so the variables impacting the longevity of the system differ as well from system to system. This is a good question to discuss with your Installer.
A “starter” is not needed for bacterial action to begin in a septic tank. Many bacteria are present in the waste material discharged into the tank and will thrive under the growth conditions present. Additives should not be used; since they are of no benefit and some may do great harm. Additives that cause the accumulated sludge in the tank bottom to increase in volume will result in the sludge being flushed out into the drainfield, plugging soil pores. Other additives, particularly degreasers, may be carcinogens (cancer causing) or suspected carcinogens that will flow directly into the groundwater along with the treated sewage.
It is not recommended to plant trees on the mound. First of all you do not want to dig up the treatment area and disrupt the construction of the mound. Also, root growth in the mound may impair it ability to do it job. The best idea is to seed or sod a mound, as well as any other treatment area, and keep the area mowed. Trees, shrubs, or flowers can be planted at the toe or base of the mound at the original grade.
The maintenance cover must be left at grade level. The reason for this is to insure there is immediate access to the tank in the case of a switch or pump failure. You can camouflage the cover with a decorative planter or a mock rock or other landscaping products as long as the cover remains accessible year round.
Common Questions Asked of the Inspector SSTS Professional
For existing systems, the inspection must include a determination that: 1) the sewage tank is watertight which most often requires pumping the tank out prior to inspection; 2) that there is no sewage surfacing or back-up in the house; 3) there is at least 2 feet of vertical separation distance from the bottom of the soil treatment system area to saturated soil or bedrock (three feet for systems built after April 1, 1996 or in shoreland or wellhead area or serving a food, beverage or lodging establishment); and 4) there is no imminent public health threat. Check with your local unit of government about inspection requirements when a property transfer is going to take place. In some areas, if the existing system does not meet compliance, the Owner of the house may be required to install a new system. It is important to know what your responsibilities are before you list your home.
The inspection of new systems includes the inspection of tanks; pump(s); the sewage treatment area; system sizing; setbacks to wells, waterlines, property lines, etc.; materials; and the vertical separation.
Typically the issuing unit of government will require a copy of the complete design which has been prepared by a licensed Designer, including the soil boring data, percolation test results, and details of the new system design with a sketch. Many issuing units of government require the Installer to apply for the permit. Additional information that may be required could include verification of the well depth by a licensed well installer, a lot survey, and/or copies of the Designer’s and the Installer’s license(s).